GORE® Joint Sealant
Versatile and easy-to-install, this 100% ePTFE sealing cord is a cost-effective solution for large steel flanges in general-use applications.
Contact Us
United States
+1 800 654 4229
Australia
+61 2 9473 6800
Brazil
+55 11 5502 7800
China
+8621 5172 8299
France
+33 1 56 95 65 65
Germany
+49 89 4612 2215
Hong Kong
+852 2622 9622
India
+91 22 67687000
Italy
+39 045 6 20 92 50
Japan
+81 3 6746 2600
Korea
+82 2 393 3411
Netherlands
+31 13 507 47 00
Poland
+48 22 6 45 15 37
Scandinavia
+46 31 706 78 00
Singapore
+65 6733 2882
South Africa
+27 71 467 7710
Spain
+34 93 4 80 69 00
United Arab Emirates
+971 2 5089444
United Kingdom
+44 1506 46 01 23
Overview
GORE Joint Sealant, the first form-in-place gasket material, was invented by Gore more than 50 years ago. Since then, this high-temp rope gasket material has proven successful in sealing steel flanges with large diameters, rectangular or irregular shapes, and rough or pitted surfaces.
When compressed, this soft, conformable cord forms a thin yet strong seal. This high-temp rope gasket material is also a chemical-resistant joint sealant that will withstand challenging process conditions and aggressive process media. It can also seal applications where available bolt loads are low, or in applications that demand a gas-tight sealant.
GORE Joint Sealant is a versatile general assembly sealant for many Maintenance, Repair and Operations (MRO) teams because it seals reliably — and because this form-in-place seal is easy and cost-effective to install. For most applications, just peel off the adhesive backing, apply to the surface, and overlap the ends. (For more complex applications, see our installation instructions.)
Of all the joint sealant types, this durable industrial sealant is surely one of the easiest and most versatile solutions for a wide variety of gasketing applications.
Applications
Processes using highly-aggressive media:
- Chemical processing
- Pulp and paper
- Mining and minerals
- Semiconductor manufacturing
- Power generation
Processes requiring an expanded PTFE joint sealant material:
- Those that demand a high-temperature joint sealant
- Those that employ highly-corrosive media
- Those that need a gas-tight sealant or vacuum gasket cord
Large and/or non-standard steel equipment flanges:
- Tank manways
- Handholes and manholes
- Ductwork
- Housing covers
APPLICATIONS FOR GORE JOINT SEALANT

GORE® Joint Sealant creates form-in-place gaskets that reliably seal steel flanges in ducting, columns, turbines, mixers and tanks.
Performance Benefits
WHAT MAKES GORE JOINT SEALANT SO VERSATILE?

Gore’s expansion technology creates fibrils that enable GORE Joint Sealant to seal irregular flange surfaces more reliably.
Gore’s expanded polytetrafluoroethylene technology
GORE Joint Sealant is made of 100% monoaxially expanded PTFE (ePTFE), using Gore’s expansion technology to create a high degree of fibrillation.
High fibrillation is what improves the joint sealant material’s strength and seal performance, and creates the soft, conformable surface that readily fills minor flange irregularities.
GORE Joint Sealant is versatile enough for use in strong alkali-, acid- and solvent-based chemical process systems, as it is chemically resistant to all media (pH 0-14) except molten/dissolved alkali metals and elemental fluorine.
HANDLING AND INSTALLATION? SIMPLICITY ITSELF
GORE Joint Sealant is an easy, cost-effective solution for a wide variety of sealing and gasketing applications.
This rope gasket material can instantly be formed in place to fit any shape, regardless of flange size or complexity, or flange condition. It offers installation options for fragile flanges, and for applications where flange rotation must be minimized or prevented.
Supplied on a spool, this expanded ptfe joint sealant is fast and easy to install:
- Peel away the convenient backing strip.
- Apply the adhesive-backed sealant to the flange.
- Overlap the sealant ends to form a durable and reliable gasket.
With GORE Joint Sealant, even sealing vertical flanges is a one-person job.
» See how easy it is to use GORE Joint Sealant: view our Installation Guide |
AN IMMEDIATE AND COST-SAVING SOLUTION
When time is money, Gore can help you save both
With GORE Joint Sealant, creating custom large gaskets on the spot is swift and simple, because your form in place gasket is immediately available. No need to wait for one to be fabricated off-site. No need for extra gaskets-and-seals procurement efforts to receive pallets, or requisition trucks or crane-lifts. No need for special handling or maintenance required, either.
Gasket creation and gasket installation are faster and easier with GORE Joint Sealant. Its tight, durable seal means maintenance is minimal, too. With fewer interruptions and less downtime, productivity is higher all around — and so are the related cost savings.
Technical Specifications
Test Data
Gasket Design Factors
CERTIFICATES & APPLICATION INFORMATION
Resources
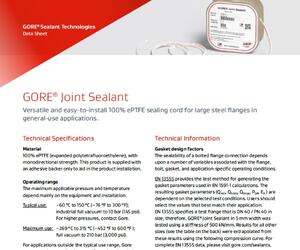
Data Sheet: GORE® Joint Sealant
Data Sheets, 152.87 KB
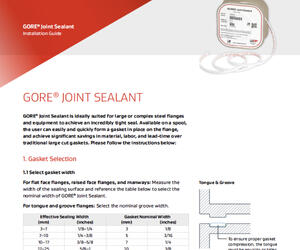
Installation Guide: GORE® Joint Sealant
Installation Guides, 570.1 KB
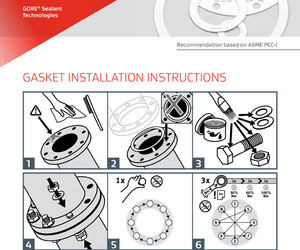
Installation Guide: Bolted Flange Assembly Instructions
Installation Guides, 134.14 KB
FOR INDUSTRIAL USE ONLY
Not for use in food, drug, cosmetic or medical device manufacturing, processing, or packaging operations.